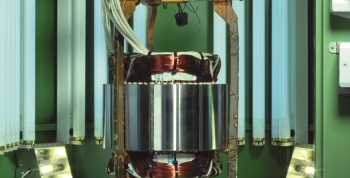
To start the Hot-dip UV process firstly the machines winding should be preheated by current. The correct pre-heat temperature is achieved by application of differing levels of current depending on the size and the dimension of the winding / machine. With winding at a temperature in the range of 130 – 150°C the parts are normally dipped into the resin for 1-2 minutes and then drained for 5-10 minutes.
For resins without potentially explosive monomers the current heating could be maintained during the dipping and drainage process. Curing is also achieved with the use of current heating. The additional exposure to UV rays for approx. 2-4 minutes provides for rapid curing of the exposed areas of the machine core, the tying tapes, as well as other insulating materials. With this process method short cycle times and a complete filling of the winding can be achieved. Additional cooling of the resin tank should be ensured to guarantee sufficient tank stability.