Automotive, consumer, aircraft as well as construction industry are making use of electronics which are subject to continuous transformation: more miniaturization, flexibilization having internet of things in view are just some of those continuous trends. Typical examples for such technologies are membrane switches, displays, RFID-tags, printed heating, printed electronic circuits, flexible electronic boards, flexible photovoltaic cells or in-mold electronics.
The reason for the intelligence of electronics and thus its continuously growing application consists in connecting components with electronic circuits. Surface Mount Device (SMD) technology has developed over the past decades in electronic industry as the dominant technology. Soldering with solder paste is the state-of-the-art process to connect electronic components such as sensors, processors, or light emitting diodes (LED) with an electronic circuit substrate. In today’s technology these substrates are typically FR-4 boards made of fiber re-enforced epoxy resin.
In printed electronic standard substrates are made of Polyethylenterephatalate (PET) or Polycarbonate (PC). But how to perform a solder process if the substrate is made of such temperature-sensitive thermoplastics now? PET and PC will not survive 150°C in process. What if the components cannot cope with the high temperatures of a soldering process of 200°C and higher? What if environmental requirements are asking for low energy process and sustainability requirements are requesting for less metal in process?
The answer to these questions becomes the so called “low temperature soldering” or solder alternative “electrically conductive adhesive/ECA.
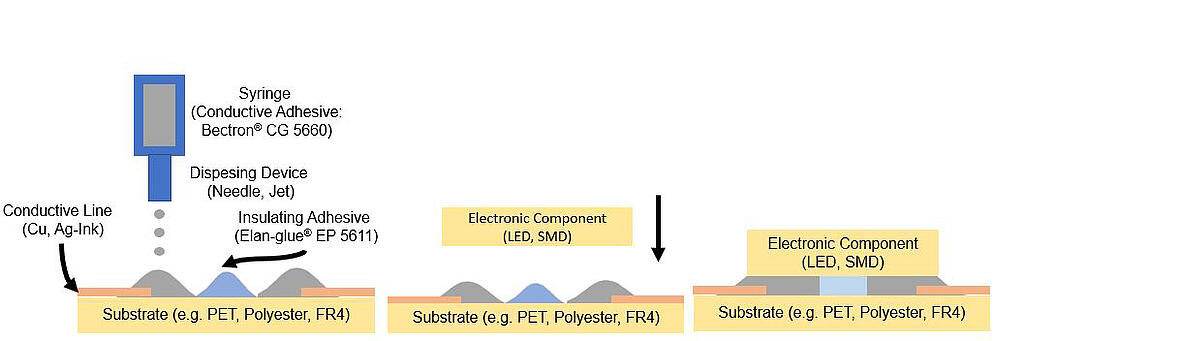
This type of adhesive is formed of a resin and silver pigments. The resin keeps the silver in place and realizes the mechanical bonding between the component and the substrate. The silver is providing the necessary electrical conductivity to realize the electronic connection. Silver is especially useful coming with an intrinsically high electrical conductivity and a reduced tendency for deterioration due to oxidation. Furthermore, silver oxide is also electrically conductive. These three aspects are compensating for the costs of the precious metal used.
ELANTAS Europe is having proven experience in developing resin for electrically insulating application and designing conductive inks for printed electronics. Combining these two competences results in a powerful electrically conductive adhesive: Bectron® CG 5660.
Bectron® CG 5660 represents a single component adhesive based on epoxide chemistry with thermal cure. Bectron® CG 5660 comes with a high electrical conductivity (surface resistivity: 300-400 mW/Sq/mil; volume resistivity: < 1 • 10-5 W • cm). Bectron® CG 5660, despite being a single component epoxide material, has shown stability in the uncured state at 20°C for months without changing adhesion or electrical conductivity in the final product. The epoxide chemistry provides good adhesion on most substrates such as other FR-4-boards, PET, PC and metal, hence typical materials which are requested to be bonded with electronic components. Different curing schemes have been explored for Bectron® CG 5660 successfully already in various applications. Cure times range from 10 min, 130°C on a thin PET foil in a conveyor system to 60 min at 90°C on a heavy steel plate in a batch furnace. All together the impact of heat becomes much lower than in case of a classical soldering process. The Bectron® Team is ready to support you to identify your specific cure scheme!
Up to approx. 135°C the material exhibits a low thermal expansion coefficient (Tg = 135°C, CTE: 40 – 80 ppm/K). This is a good starting point to withstand thermal shock events under standard application temperatures up to 125°C. In thermal gravimetric analysis (TGA) a small sample is heated up with a rate of 10 K/min in a chosen atmosphere (i.e. air) and the weight is continuously recorded. Figure 1 shows the of Bectron® CG 5660 under air. Under these conditions of TGA even at 200°C, one cannot observe any significant change in weight which could be related to decomposition or outgassing.
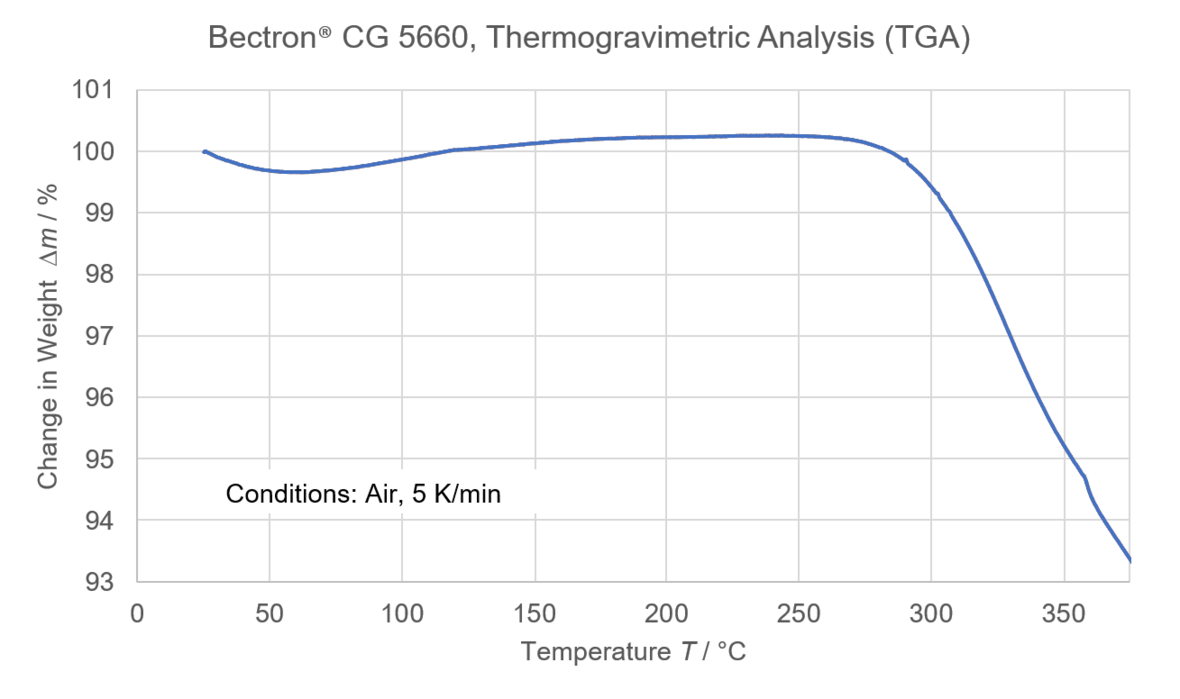
In addition to the above-mentioned properties Bectron® CG 5660 comes with a significant thermal conductivity (> 6 W/m K) which makes this product especially interesting as a thermal interface management material (TIM) to transfer heat from a component of a board to a heat/cooling sink.
Different application methods have been explored successfully with Bectron® CG 5660, ranging from screen printing, stencil printing and dispensing dots down to 100 – 500 µm.
Bectron® CG 5660 applied by screen printing Bectron® CG 5660 applied by jetting
Bectron® CG 5660 is made to create connections in different aspects: In the classical electronics the material provides simple connections, adheres components and supports heat dissipation. In printed, flexible in-mold electronics Bectron® CG 5660 creates the connections between the conductive network and the working components. In semi-conductors it might be useful as for die-attach and for conductive chip-bonding.
For questions about the choice of appropriate materials or application-specific topics, please feel free to contact us directly under advancedPrinting@ altana. com
Learn more about our portfolio for printed electronics.