Email us on advancedPrinting@ altana. com
Printed conductor paths made of polymer-based, silver-filled printing inks are light and flexible and can be applied in an additive process by printing. As a result, such polymer pastes can be applied to a variety of substrates, rigid or flexible. The screen printing process is usually the method of choice here, as thick layers can be applied for good conductivity and mechanical stability. Screen printing is also a robust process that can easily be used to economically produce medium quantities of several tens to hundreds of thousands of units.
The UV silver ink developed by us is based precisely on this economic calculation of the process. Conventional silver printing pastes usually need a few minutes drying/curing time at 120°C or more. In process planning, this is usually the obstructive step that slows down the actually fast and economical screen printing process and the root of high energy costs. An UV-curing printing ink "dries" within seconds when exposed to suitable UV radiation, thus increasing the achievable printing speed enormously.
This is made possible by the functional principle of such a printing ink. In contrast to a solvent-based ink, in which a polymer is dissolved and simply dries physically by evaporating the solvent, which costs time and energy, an UV-curing printing ink consists of a mixture of reactive polymers dissolved in so-called reactive thinners. Photoinitiators are added to this mixture, which are able to cause the mixture to react by stimulation with UV radiation. This means that no solvent has to evaporate, but the entire mixture is reacted and cures. These 100% systems result in thicker films and, due to the cross-linking, also in more stable films. This completely different drying principle results in some advantages, but also in things that have to be considered during the application to guarantee the success of such an UV ink.
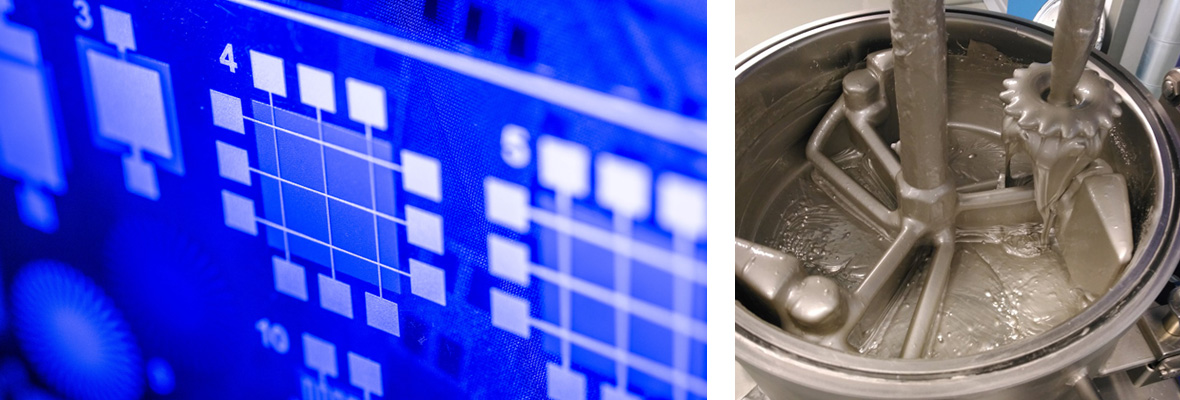
As already mentioned above, one of the essential advantages is the higher curing speed, as the described reaction takes place very fast. Especially for printing speeds in roll-to-roll processes this advantage is almost indispensable.
Of course, the extremely low solvent content is also very clear advantage with regard to the increasingly important emission values. In many industrial sectors, solvent-based systems are being pushed further and further into the background due to environmental pollution and the corresponding legal framework. UV-curing printing inks represent a contrasting and more sustainable approach in terms of both environmental and economic aspects.
With conventional, solvent-based printing inks, screen life is limited by evaporating solvent. Slow printing speeds are particularly susceptible here, as the printing ink forms very thin films in the meshes of the screen, allowing the solvent to escape easily. After a certain period of time, this leads to fluctuating printing results in the printed image, with the meshes sometimes running completely taut or the edges becoming blurred. Especially when it comes to electrical conductivity, this naturally also causes fluctuations in conductivity, which makes the design of circuits correspondingly difficult.
An UV-curing printing ink does not have this problem. The reactive components used hardly evaporate at all, which ensures excellent screen life times and print reproducibility. However, it is essential to ensure very good shielding from UV light, which would otherwise cause a reaction on the screen. Small amounts of UV dose e.g. through window glass or even from conventional ceiling lamps can already be felt here and lead to similar effects as evaporation of solvent. Here, too, the ink seems to "dry up", whereby this is a thickening as a result of the reaction triggered. By the way, this problem can easily be solved by using appropriate filters on the ceiling lamps which filter out the UV radiation. With heavily filled systems such as the UV-curing silver ink Bectron® CP6671, this problem is usually much more pronounced than with UV-curing insulators, for example. This is due to the photoinitiators used, which usually absorb in a wider wavelength range up to blue light and can be made to react. This is necessary because longer wavelengths (red-shifted) are transported further through the material thus are needed for curing the deeper layers. This effect is analogous to the finger appearing red when shining light of a white lamp through it.
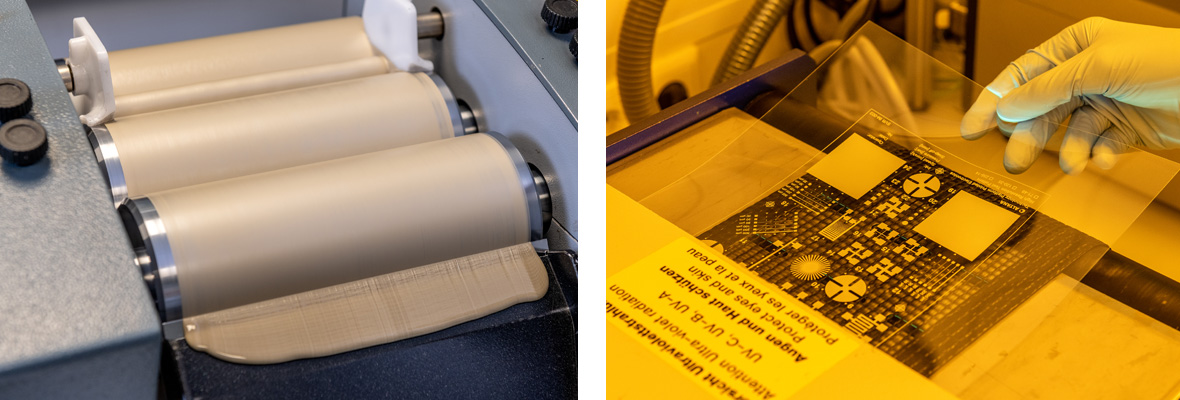
During the drying process, this reaction should of course take place as quickly and efficiently as possible in order to achieve a perfect result. It is important that the UV lamp used delivers a sufficient dose (output per time) in the right wavelength range for the photoinitiators. The Bectron® CP6671 silver ink has been developed for use with mercury vapour lamps without additional doping. Doped lamps are also possible here, but may require adjustment of the necessary dose. Our sales experts will be happy to help you here.
The adjustment of an UV-curing conductive silver printing ink certainly poses an enormous challenge for the ink development, as evaporating solvent in a solvent-borne ink naturally causes the remaining film to shrink, which ultimately causes the particles to come together more closely. Film errors caused by printing are also often corrected by oven drying. With the Bectron® CP6671, we have succeeded in overcoming these disadvantages so that you can concentrate completely on the advantages mentioned above with this product and still obtain excellent, error-free print quality with very good conductivity.
Contact us, convince yourself and do not hesitate to ask for a sample.
For any questions about the choice of appropriate materials or application-specific topics, please contact us advancedPrinting@ altana. com
PDF DOWNLOAD
Learn more about our portfolio for printed electronics.