Printed Electronics has been a buzz word for quite some time now and is used in different industry sectors, ranging from consumer electronics to IOT devices.
However, bringing an idea to a market ready product is not as easy as it seems, especially when you are looking at the environment of the product, or the specifications that must be met. How do you deal with abusive or sensitive environments, limitations in size and/or conductivity, production time, product integration, etc.?
Needless to say, - it is one thing to create a demonstrator, but it is a totally different thing to bring that demonstrator into a market ready state, going through the different steps of product evolution.
In a close and unique cooperation with our customer Mentech, Metafas co-developed a washable and durable smart garment which measures electrodermal activity for early stress recognition at mentally disabled people. The application targets to improve the quality of life from patients while at the same time it reduces significantly the workload of healthcare. The talk will guide you from the concept development to the mass production today, including the technical features of the printed electronic sensor and improvements we have made recently.
Printed electronics have several key advantages in comparison to traditional electronics. Transparency and flexibility are two major advantages known in public and used in many applications. At Kundisch we have progressed from flexible hybrid electronics with complex electronic circuitry on flexible films to transparent flexible electronics. This enables new application similar to the once in science fiction movies. This new technology will be used for customized solutions within the HMI industry but also bridging to others such as aviation or medical industries. Transparent flexible electronics yield many advantages compared to state of the art solutions on the market.
Conventional electronic industry is based on Printed Circuit Board (PCB), in which different electronic components are picked and placed on a PCB. These different components are produced by different suppliers and assembly is done by an assembly company. Unfortunately, similar production approach is being applied in Printed Electronics i.e. Printed Electronic components are produced by different suppliers and then assembly is done by a specialized assembly company. But the actual beauty of Printed Electronics lies on printing all electronic components directly on a single substrate. This integrated printing, let us call it “Printegration”, can make high volume production of Printed Electronics a reality. During the presentation, different applications by combining different printed devices – battery, sensors, electrochromic display, antenna – will be explained.
This presentation is intended to provide an insight in the subject of printed electronics and functional products in the CCL Design Group. On the basis of current development and production trends as well as the approach of the companies operating within the group in this field of activity, some of the opportunities currently offered by the market and demanded by customers will be highlighted. Using tangible examples, the implementation of digital concepts as well as cooperative developments in the areas of HMI, printed heaters and batteries can be demonstrated.
Dr. Andreas Willfahrt
Application Engineer Intelligent Labels
CCL Design Stuttgart GmbH
Jonas Breuer
Managing Director
CCL Design Stuttgart GmbH
The field of printed electronics has witnessed significant advancements in recent years, leading to the widespread adoption of various applications in the mass market. This presentation aims to provide a focused perspective on the development of high uniformity and free form printed heating elements. Additionally, introducing transparency into these heating elements presents tremendous potential for future applications. The talk will delve into the possibilities and advantages of this combination, highlighting its impact on diverse industries such as such as automotive, aerospace and healthcare.
In addition to the discussion on printed heating elements, the presentation will also showcase other noteworthy applications. One such application is BaMoS, a cutting-edge system designed for battery monitoring. The audience will also gain brief insights into the latest developments of rPCB (real Printed Circuit Board).
TactoTek, with its forerunner manufacturing technology (IMSE®) injection molded structural electronics, revolutionizes the way smart surfaces are designed, manufactured and experienced. IMSE® integrates printed electronics and conventional electronic components inside 3D plastic parts by reducing the thickness up to 90% and weight up to 80%. Additionally the number of parts is significantly reduced and thus the whole assembly is simplified. In this presentation, the current state of IMSE sustainability is introduced and further improvements including incorporation of alternative materials and technologies for IMSE are being presented.
Plastronics, or In Mould Electronics, covers a wide variety of applications. However, interior vehicle design has recently developed a very strong interest in IME. The main objective is to have direct impact on the manufacturing value chain, and therefore incorporating new advantages over the current traditional procedure. From reducing the assembly time of the parts to the ability of encapsulating the electronics and dramatically reducing the weight and thickness of the part, giving birth to a more sustainable solution by reducing the quantity of raw material employed during the fabrication. This whole process is focused on implementing a functional electronics design into the 3D part itself using adapted conventional industrial processes, such as screen printing, surface mounting of electronic components, thermoforming, trimming, and injection molding. This union of processes offers the possibility of creating new parts with extended functionalities, such as lighting and sensorization, in turn allowing to generate a deeper interaction with the user. Welcome to the revolution of Smart Plastics.
Flexible and printed electronics are increasingly penetrating a wide range of industries, including automotive, consumer electronics, healthcare, printing/packaging and smart buildings, as well as its growing presence in the Internet of Things (IoT). Thin, lightweight, flexible and robust are the key features of this technology, which can be seamlessly integrated into a wide range of products.
This presentation will introduce the new OE-A roadmap. This roadmap is a collaborative effort among OE-A members that captures the current state of the art, identifies key challenges, and provides an outlook for future product generations.
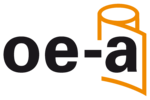
Dr. Klaus Hecker
Managing Director
OE-A (Organic and Printed Electronics Association)
A working group within VDMA
In this talk first the target of PV electricity generation will be elaborated and the efficiency development at Qcells presented. In the main part the talk will give insights into the metallization of silicon solar cells, its current status as well as development trends. Finally metallization challenges for next generation tandem solar cells under development at Qcells will be discussed.
With further up-scaling of emerging photovoltaics like perowskite/silicon tandem solar cells worldwide, the reduction of precious materials namely Ag and the utilization of low-temperature approaches is gaining major attention. Flatbed screen printing is expected to remain the dominant process for metallization due to cost-effectiveness and flexibility towards a fast-evolving PV market. However, three aspects will be crucial for its long-term success: Firstly, further reduction of screen-printed finger widths remains one of the key objectives to further decrease paste consumption and shading losses. Secondly, shifting the metallization process towards alternative materials e.g. Copper based pastes whilst maintaining the fine-line printability of Ag contacts. Third, improving uniformity of contacts and their curing behavior to enhance overall paste utilization (Grid conductivity vs. paste laydown). Herein, the talk will give a scientific insight into the approaches and recent results within the cooperative work between ELANTAS and Fraunhofer ISE along with their industrial potential.

Berit Schuster
Head of R&D Printed Electronics
ELANTAS Europe
Dr. Roman Keding
Head of Group "Process Integration - Structuring and Metallization
Fraunhofer Institute for Solar Energy Systems ISE
Organic photovoltaics (OPV) is a technology that can benefit from both Roll-to-Roll and wet processing; using liquid inks to create a photovoltaic device. While printed OPV is not yet ready for outdoor solar applications, there is another market where this technology can already be utilized, namely the indoor PV market (IPV). A key driver for this market is the ongoing sensor boom ever-increasing demand for more data and hence devices that collect this data. A major limiting factor in deploying an abundance of these sensor devices is the cost for keeping track of and replacing batteries; the “battery hell”.
Thomas Österberg, RnD director at Epishine, will discuss the key points that enables the Epishine process to deliver high performance and yield, as well as give a status update on the company at large.
Printed electronics promise to bring electronic functionalities on any substrate through deposition techniques borrowed from graphic arts. Yet, the peculiar features of electronic architectures and printable inks often require to move away from the initial promise when it comes to set up production ready processes. Device encapsulation, the limited conductivity of transparent electrodes and expected performance and durability are the key limitations hindering from keeping the promise of being able to really print on any surface at an industrial stage. Ribes Tech is an Italian company devoted to printed electronics and organic photovoltaic specifically who set up a semirotative printing line for OPV production and more. In this talk we would like to share some considerations that we discovered in our development process on the goal of being able to produce OPV rolls without relying on vacuum processes or etching steps.
In this Airbus vision we show how printed electronics technologies could affect the manufacturing of aircraft, from the first talks with airline customers all the way to the end of life of aircraft products.
The adaptation of customer needs has a major impact on the following engineering and manufacturing phases. We demonstrate how a significant technology change can influence and transform the huge customization challenge into a unique selling point and still reduce labor hours and cost in manufacturing and final assembly. We also show how future services and maintenance, repair & overhaul can be affected beneficially. Additionally, all these improvements are environmentally friendly since the architecture, which is enabled by the printed electronic technology, supports recycling and circular economy far more than current applications can. After a brief glance into the near future of the project we will enter a fruitful dialogue.
Surface Lighting has the ability to change the world of design and change how we interact with products around us. It is a game changer for the printed electronics industry, since light and visual interfaces are becoming a part of any product. We are becoming completely depended on light as a indicator and design element, that communicates ambience, emotions, and statuses.
Today Visual Interfaces have to be assembled through the hybrid electronics approach. LEDs are picked and placed and covered with light guides to achieve the target shape and form. Technologies like this maybe cheap to manufacture in mass, but they are hard to setup and to incorporate and any adjustment in shape requires additional setup costs and time.
Surface lighting is paper-thin and thus has no space requirements. Affordable Surface Lighting technologies so far have been also accompanied with draw-backs of complex driving electronics, large size or lack of brightness. A technology that can meet all of this is OLED. OLED are made in process that are similar to the chip manufacturing industry. This makes them expensive in unit cost and even more in setup.
Thus the dream of Light Everywhere, OLED Everywhere vanishes quickly on hard economical reality. Inuru has simplified the way OLEDs are manufactured by not taking the material into vacuum to to evaporate them, but taking the molecules and printing them. We are utilizing state of the art ink-jet technology used for color printing today.
The infrastructure we use for an output of 8M panels require a fracture of the space than conventional evaporation processes. The additive manufacturing of ink-jet allows us to save materials, reduce cost and print any shape in real time, on demand like color.
We are 3D printing lighting on a nano-meter precision. This technology will revolutionize the electronics manufacturing and will open printed electronics industry to a wider audience.
The market for drying systems will change overall in the coming years. Energy and emissions are key drivers (climate protection). Lambda technology´s digital drying technology offers an answer to the growing demands. The very flexible and targeted use of modular hybrid elements of NIR and IR with air works for a variety of materials and surfaces.
This technology also opens faster and more efficient processes in the field of printed electronics. In cooperation Lambda Technology and ELANTAS have been investigated the application of Hybrid drying technology for ELANTAS printed electronic products. The technology as well as the results collected so far in the collaboration will be presented in a joint presentation.